Eco-designing our watchmaking case
Every modern, responsible company must limit its environmental impact. Nowadays, updating our ways and reconsidering our production methods has become mandatory.
For example, the production of 100,000 “classic” watch cases has the same impact as the average yearly consumption of 23 European citizens.
Here at FPM, we went through the process of rethinking our “classic” watch case by looking at it through the lens of eco-design. This simple, effective method clearly reveals every inch of leeway available to us in reworking exceptional packaging for minimal impact.
We prepared a concrete demonstration.
Product Life Cycle Analysis
To establish a product’s environmental impact, we use the Life Cycle Analysis (LCA) method. We begin by breaking packaging down to its components and analyzing each individual element to find out which is the most polluting. Next, we determine our levers across everything from packaging design to production, shipment, and product end of life.
Our case study revealed that raw material accounts for 82% of the product’s final impact.We observed that, in relation to the amount used (i.e., the product’s weight), the most environmentally damaging materials were plastic (PS) and galvanized steel.Despite the fact that galvanized steel makes up only 3% of the packaging, it creates 31% of the overall CO2 footprint. Plastic (PS) represents 83% of the pack’s weight and generates 50% of its emissions. le plastique (PS) représente 83% du pack et en génère 50%.
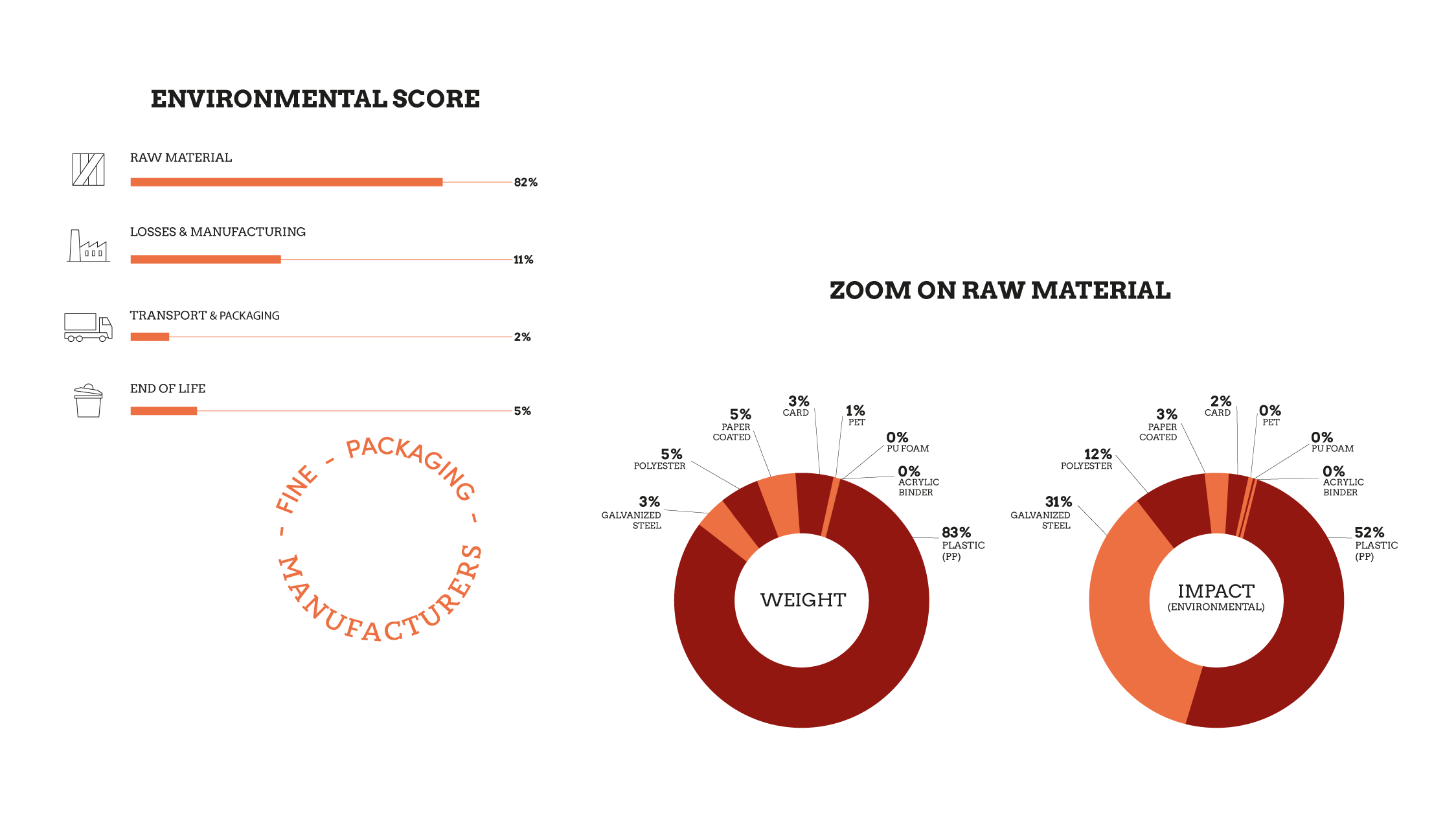
Simplifying a high-end pack’s composition
We now know that the watch case’s design is a response to specific aesthetic traditions and manufacturing practices, like calibration tools, materials, buckles, etc.
We have to break with tradition in order to reduce our impact, simplify the pack’s complexity, and find alternative materials.There’s a delicate balancing act between trying to alter a design while keeping the product’s perceived luxury value, using visual, sensory cues as well as ergonomics, weight, feel, sound, and more.
Our eco-friendlycase offers a similar, yet simplified structure, that minimizes the materials used and makes assembly and recycling easier.
We’re replacing our usual materials. Here, the buckle’s leather tab gets swapped out for reconstituted leather. Plastic is substituted with bioplastic. With the DIAM Group’s support, our research on sourcing alternative plastics est un engagement déterminant pour limiter notre impact. Aussi nous réduisons le poids de l’acier galvanisé de 5g tout en le compensant par le poids du bioplastique.
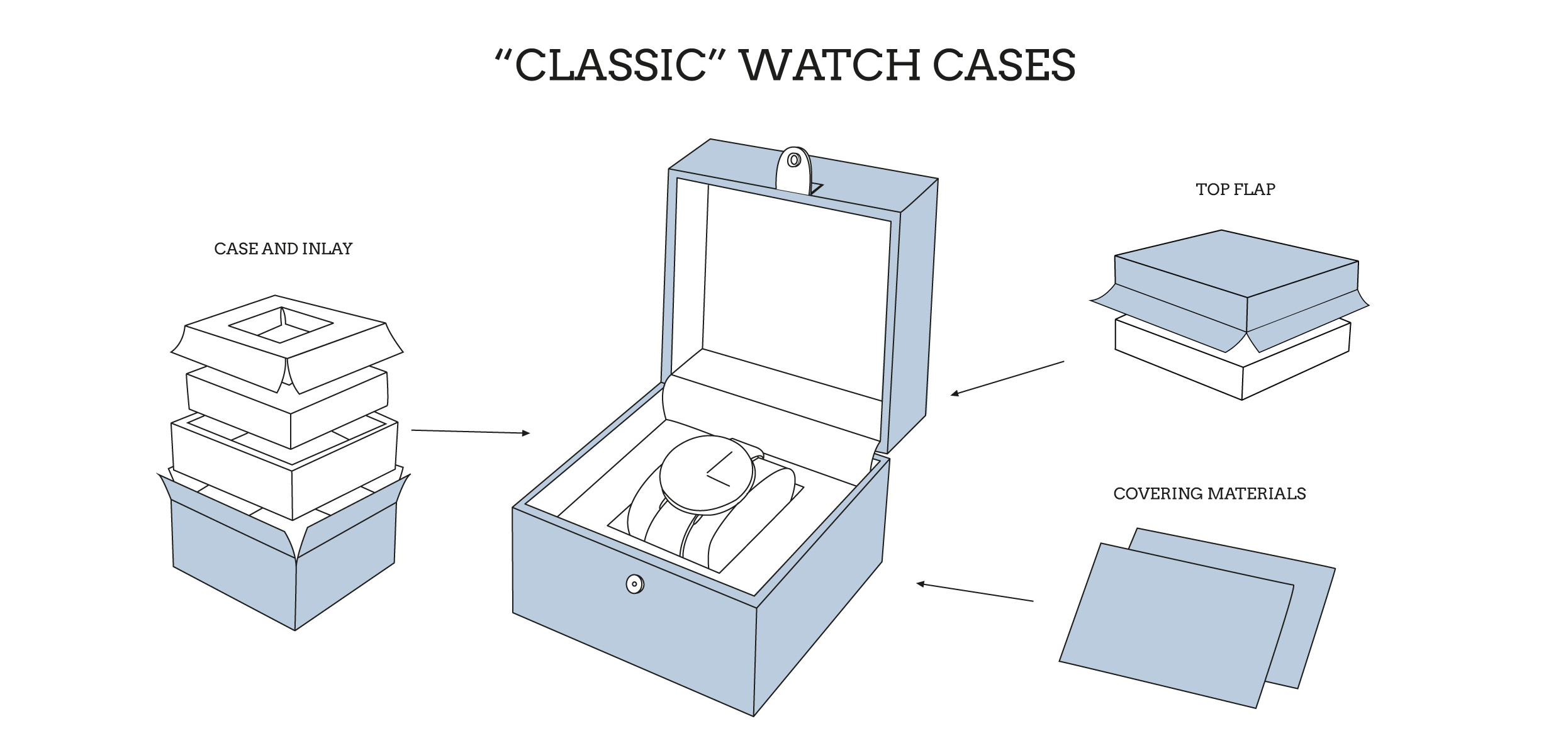
Eco-design as a whole
Reconsidering the case from the design up allows us to propose alternative materials, balance out volumes, reduce the weight of our highest-impact materials, reduce gluing, and rethink opening/closing mechanisms.
Offering innovative and eco-friendly designs also means optimizing the product’s end of life by creating structures that can be taken apart, thereby making recycling and product reuse easier. We can also deploy other levers like reducing excess packaging and shipping.
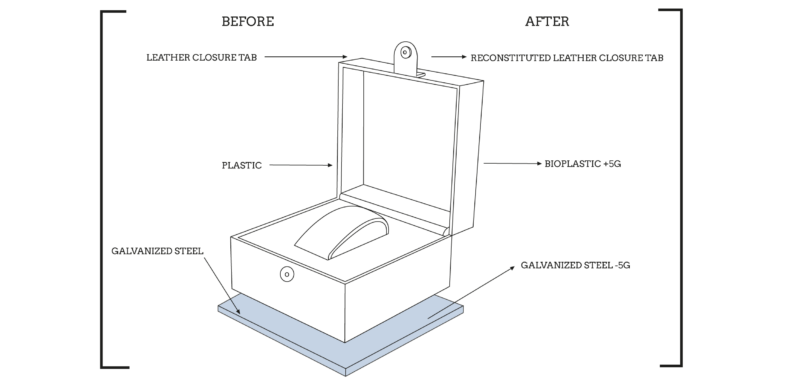
Here at FPM, we believe that the packaging of tomorrow must be green at all costs.
Here’s to the environmentally friendly projects of the future!
FPM teams